

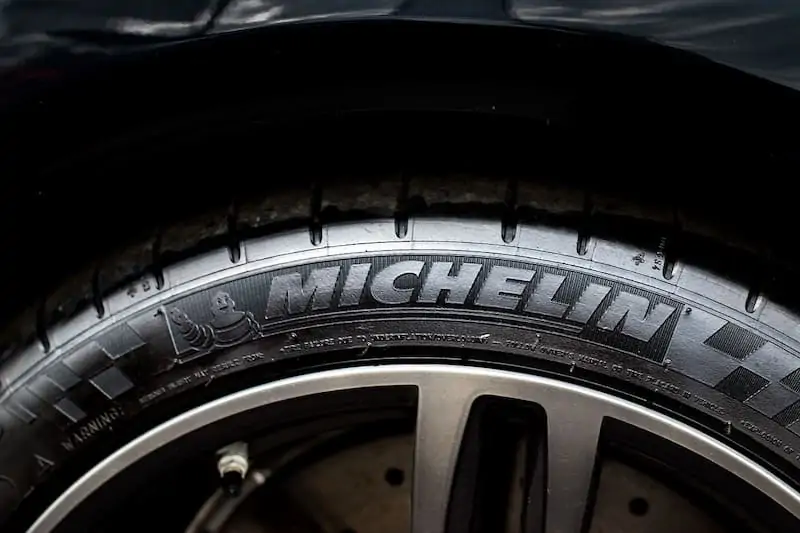
The line of action of the (aggregate) vertical force no longer passes through the centers of the cylinders. The resulting pressure distribution is asymmetrical and is shifted to the right. In this case this decreases the pressure that is needed to keep the two bodies separate. This is again resisted by the hysteresis effect. Later its vertical deformation is decreasing. Therefore, an additional pressure is generated to avoid interpenetration of the two surfaces. Initially its vertical deformation is increasing, which is resisted by the hysteresis effect.
#R284 ECOPIA VS XLINE ENERGY Z ROLLING RESISTANCE PATCH#
Consider a particle that enters the contact area at the right side, travels through the contact patch and leaves at the left side. In the absence of surface friction, contact stresses are normal (i.e. If two equal cylinders are pressed together then the contact surface is flat. This main principle is illustrated in the figure of the rolling cylinders. Hysteresis is the main cause of energy loss associated with rolling resistance and is attributed to the viscoelastic characteristics of the rubber. As the tire rotates under the weight of the vehicle, it experiences repeated cycles of deformation and recovery, and it dissipates the hysteresis energy loss as heat. The rubber compound in a tire exhibits hysteresis. The primary cause of pneumatic tire rolling resistance is hysteresis: Ī characteristic of a deformable material such that the energy of deformation is greater than the energy of recovery. Primary cause Asymmetrical pressure distribution between rolling cylinders due to viscoelastic material behavior (rolling to the right). Sole rolling resistance factor is not dependent on speed. Also, sand on the ground will give more rolling resistance than concrete. For example, a rubber tire will have higher rolling resistance on a paved road than a steel railroad wheel on a steel rail. The losses due to hysteresis also depend strongly on the material properties of the wheel or tire and the surface. Additional contributing factors include wheel diameter, load on wheel, surface adhesion, sliding, and relative micro-sliding between the surfaces of contact. Factors that contribute to rolling resistance are the (amount of) deformation of the wheels, the deformation of the roadbed surface, and movement below the surface. Īny coasting wheeled vehicle will gradually slow down due to rolling resistance including that of the bearings, but a train car with steel wheels running on steel rails will roll farther than a bus of the same mass with rubber tires running on tarmac/asphalt.

This coefficient of rolling resistance is generally much smaller than the coefficient of sliding friction. In addition, only the so-called slip resistance involves friction, therefore the name "rolling friction" is to an extent a misnomer.Īnalogous with sliding friction, rolling resistance is often expressed as a coefficient times the normal force. Although some researchers have included this term in rolling resistance, some suggest that this dissipation term should be treated separately from rolling resistance because it is due to the applied torque to the wheel and the resultant slip between the wheel and ground, which is called slip loss or slip resistance. Note that the slippage between the wheel and the surface also results in energy dissipation.

Two forms of this are hysteresis losses (see below), and permanent (plastic) deformation of the object or the surface (e.g. It is mainly caused by non-elastic effects that is, not all the energy needed for deformation (or movement) of the wheel, roadbed, etc., is recovered when the pressure is removed. Rolling resistance, sometimes called rolling friction or rolling drag, is the force resisting the motion when a body (such as a ball, tire, or wheel) rolls on a surface. This pressure is greater towards the front of the wheel due to hysteresis. The wheel is rolling to the left at constant speed.) Note that R is the resultant force from non-uniform pressure at the wheel-roadbed contact surface. ( W is some vertical load on the axle, F is some towing force applied to the axle, r is the wheel radius, and both friction with the ground and friction at the axle are assumed to be negligible and so are not shown. Force resisting the motion when a body rolls on a surface Figure 1 Hard wheel rolling on and deforming a soft surface, resulting in the reaction force R from the surface having a component that opposes the motion.
